End-forming is a process that is used to change the geometry of a tube, typically at or near the end of the material. The process dates back many decades: once done with castings, manufacturers have now transitioned to custom, machine-forming for cost efficiency.
The most requested types of end-forming include beading, expanding, flanging, flaring, grooving, knurling, reducing and thickening. These operations can be done on a variety of part specifications and materials, including copper, aluminum, brass, steel and stainless steel.
Beading is the most popular type of end-forming. This process is commonly used for automotive and heavy truck applications where multiple tubes must be connected to join systems or assemblies. This could be a small component such as a fuel pump, or something larger like an engine block. Beading can be done with a Norma ball and flare or Marmon bead and flare. Slots are sometimes added for better joining.
Flaring is often used in combination with beading. For example, a Marmon flare is typically used to mate with a Marmon bead and clamp to complete a joint between two pipes. The inside flare surface seals with the bead in tandem with the tensions / constrains to mate the surfaces together.
Another common flare, specifically for automotive applications, is the spherical ball flare. This is used to join with a spherical ball form and clamp, similar to the Marmon bead process. In this case the flare and ball end-form accommodate a degree of angle movement. Often used for exhaust systems, this allows for minor adjustment and movement within the finished assembly.
While heavy truck has been a key driver for end-forming, other industries also rely on this technique. For example, residential and commercial water companies rely on end-forming for tubing used to transport water and waste. Refrigeration is also an area where end-forming is used to create piping for radiators. Additionally, this process is requested by recreation companies (think ATVs, boats, motorcycles, and side-by-sides), food equipment companies, aerospace, and large-scale furniture makers.
An item can be end-formed either before or after bending, depending on the part being created. If the forming work is done after bending, the tube is trimmed to the correct length to accommodate. End forming is normally integrated with other operations, such as bending and tube lasering, as a part of an overall tube fabrication project.
There are two primary machine types used in end-forming. For lower volumes, a segmented machine, or sizer, is used. The tooling on this type of equipment has eight fingers that are powered by a mechanical drawbar, which uses pulling force on the tube or pipe to perform the expansion or reduction of the end. Typically, the tolerances for this application are more forgiving. For larger volumes and tighter tolerances, spin-forming machines and progressive ram forming processes are performed to meet the critical dimension.
Specialized tooling is required for end forming. Tools are built to the form of the part needed for the application and the type of material and machine being used. Considerations such as hardness, tube end preparation, tooling coatings, and type of material go into determining tooling specifications. Various types of lubricants are used in the process, based on the materials and desired expansion.
Overall, end-forming is a desirable and efficient technique for tube fabrication. For both small and large volumes, parts can be formed for many product applications. While tooling must be customized for the job, there are advantages to working with a reliable end-former who can provide a full range of fabrication services in one facility.
This blog was co-authored by Patrick Coenen, Project Engineer, Sharpe Products, and Pat Arens, Director of Administration, Proto-1.
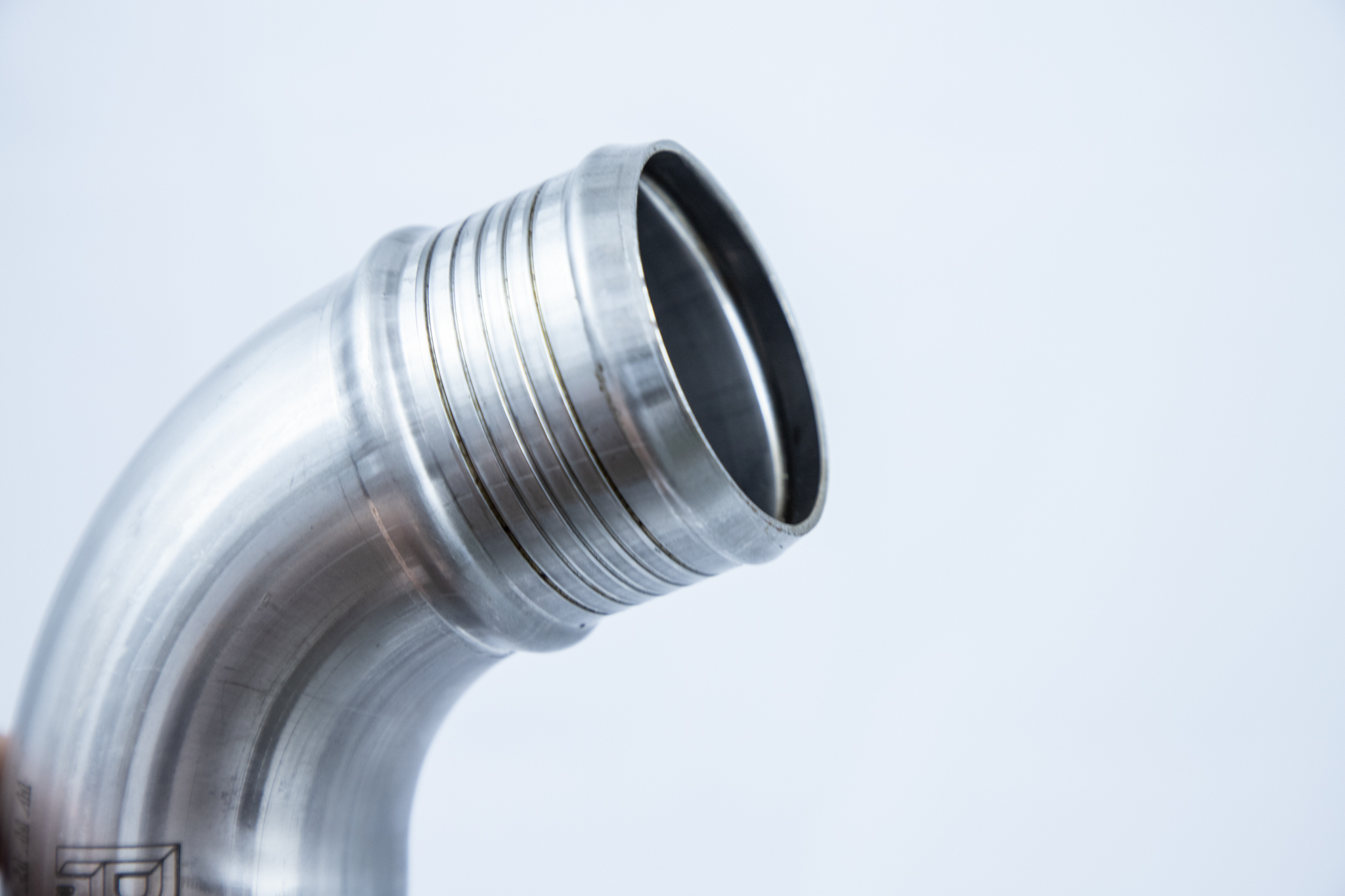
Shown above (L-R): 1.25 to 1.50" expansion, 2.5" reduction, 2.50" double aero bead and serration.